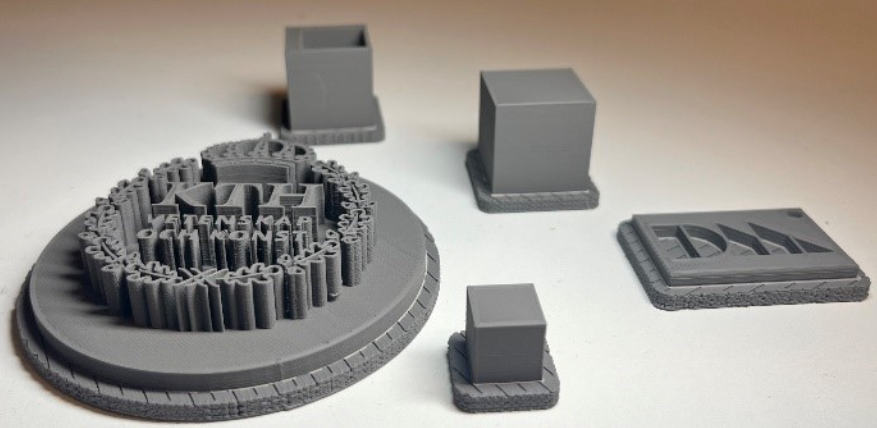
Efficient and Resilient 3D printed Magnets forAutomotive Application; A Feasibility Study (Mag3D)
The project aims at realising the feasibility of an innovative approach to produce permanent magnet components, a critical component in many electrical applications, using an indirect additive manufacturing (AM) technique called metal extrusion printing. Traditional manufacturing of permanent magnets, like Neodymium-Iron-Boron (NdFeB) used extensively in electrical motors, are limited to simple shapes (such as powder metallurgy) or they are very energy-intensive creating a significant amount greenhouse gas emissions (such as casting or powder metallurgy followed by hot pressing and hot deformation). The project, however, aids the transition to a more efficient, circular, and sustainable manufacturing process by leveraging AM (which could also strategically help Sweden/EU to reduce their magnet import from abroad). By applying this approach, we are not only hopeful to reduce the associated waste and energy consumption but also we will try to improve the magnetic efficiency of electrical motors as a system. The project aligns with the Net Zero Industry’s mission to significantly reduce the environmental footprint of the Swedish manufacturing sector while enhancing the resilience of its supply chains.