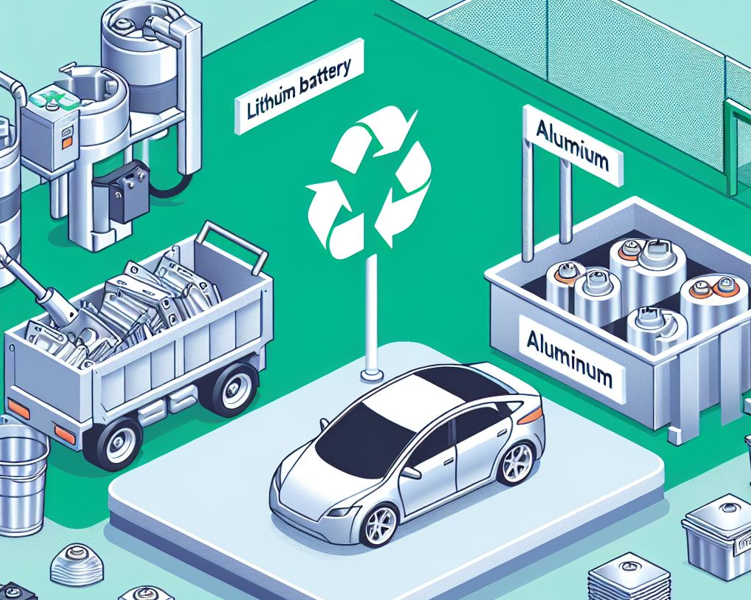
Low CO2 emission aluminium alloy battery cells produced from scrap (BAALSCRAP)
As demand for electric vehicles grows, aluminum plays a crucial role in achieving net-zero in the automotive industry. By 2030, aluminum content in a typical car is expected to reach 260 kg. However, current production of wrought aluminum alloy products (rolled and extruded) and MEGA and GIGA casting processes heavily relies on virgin aluminum from bauxite ore, an energy-intensive process with high CO2 emissions. Transitioning to a circular aluminum industry and achieving net-zero CO2 emissions requires increased use of aluminum from scrap. Currently, EV prismatic battery cell housing, one of the emerging and growing products, is made from virgin aluminum to minimize production complications, as rapid development required risk-minimized processes. However, this approach is unsustainable in the long term. Scrap-based alloys often contain elevated levels of elements like Fe, Si, Cu, and Zn, forming intermetallic phases that degrade material properties and processes such as rolling, extrusion, casting, forming, corrosion resistance, and welding. Despite these challenges, transitioning to scrap-based alloys is a necessary step for all production processes, starting now with modifications to current methods. This project aims to understand how these elements affect processes, define their limits, and identify the changes needed in production methods to enable the production of flexible alloys and drive sustainable, efficient vehicle materials.